- Home
- Paint and Substrates
PRODUCTS
Paint & Substrates
Explore Our Paint and Substrates Options
For over 60 years, McElroy Metal has been a trusted industry leader, delivering exceptional products and service to our customers.
Beyond our extensive panel selection, our employee-owners take pride in offering a variety of high-performance paint systems and durable substrate options, ensuring you get the ideal combination for your project’s needs.
Explore Our Paint and Substrates Options
For over 60 years, McElroy Metal has been a trusted industry leader, delivering exceptional products and service to our customers.
Beyond our extensive panel selection, our employee-owners take pride in offering a variety of high-performance paint systems and durable substrate options, ensuring you get the ideal combination for your project’s needs.
Request
Samples & Color Charts
Request physical samples and color charts. All items will be sent out via UPS ground unless otherwise specified.
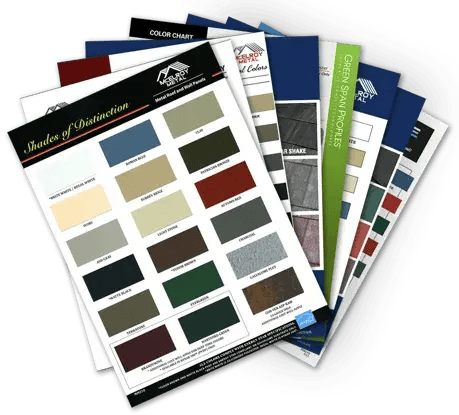
The Latest Posts on our Blogs
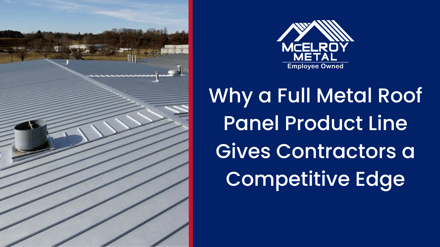
Why a Full Metal Roof Panel Product Line Gives Contractors a Competitive Edge
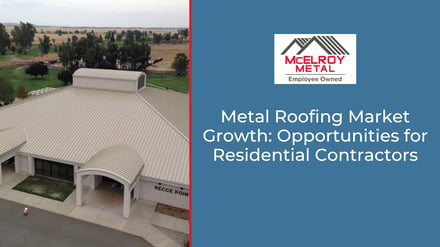