- Home
- Product
- Roof Panels
- Standing Seam System
Standing Seam Metal Roofing Products
What is Standing Seam Metal Roofing?
Standing seam metal roofing panels are attached with concealed fasteners. Originally, clips engaged with the vertical legs and were used to attach the panel to the roofing substructure. As panel options have grown, however, it is common to see clipless panels included in this product family.
McElroy Metal offers five distinct standing seam systems that can be curved on the job site, lowering transportation costs and ensuring a proper fit.
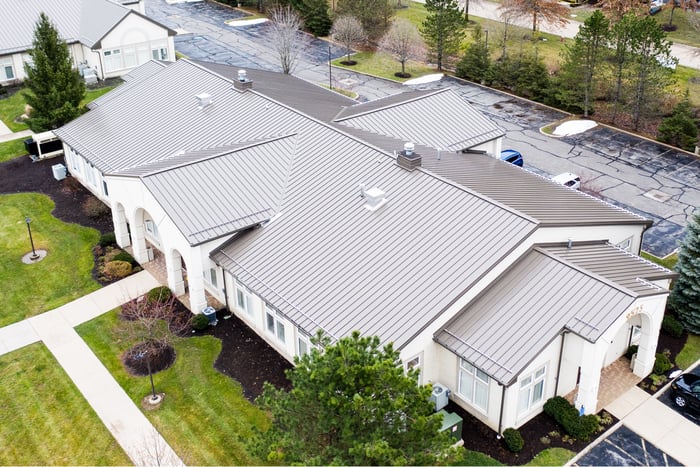
Standing Seam Metal Roofing Systems Overview
There are many nuances within the product family of standing seam. Click through the buttons below to learn more about the differences between panels and system types.
- Product Families
- Engagement Method
- Attachment Method
- Panel Styles
- Installation Approach
- Curved Roofing
Product Families
Structural
These systems are typically used on lower sloped roofs, often down to ¼:12. They are considered Hydrostatic, which means they can keep buildings watertight even when they are submerged underwater for brief periods of time. These products can be used in either open framing or solid deck applications.
Architectural
These systems are commonly used on slopes of 3:12 or greater. They are considered Hydrokinetic which means that they can keep buildings watertight while water is flowing over them as opposed to the Structural systems which can accommodate water submersion. Some panel styles in this family have load-carrying capability, others do not.
Engagement Method
Snapped
Snapped panel systems consist of a male and female leg. Once the legs are properly engaged, pressure is applied and the panels snap together to complete the installation sequence.
Mechanically Seamed
Mechanically seamed systems require the use of a powered seaming machine after panel installation to ensure proper performance.
Attachment Method
Clipless
Clipless standing systems are fastened through a pre-punched fastening flange. These flanges typically have repeating slots every 2-4” to facilitate attachment to the roofing deck, most often plywood.
Clipped
Clipped systems consist of a clip that is integrated into the male/female panel legs and is then attached to the deck or purlins.
Panel Styles
Trapezoidal
Trapezoidal panels are the most cost-effective standing seam panel style; however, due to the large trapezoidal shape, they aren’t widely used in high visibility architectural applications or those involving valley conditions.
Vertical Leg - Non Symmetrical
As the name implies, vertical leg panels have a vertical leg at the connection of the male/female leg. This family of panels can be snapped or mechanically seamed.
T Panel - Symmetrical Standing Seam
T style panels combine the look and functionality of a vertical leg but have a separate batten cap that is then mechanically seamed in place. These panels allow for the easy removal and replacement of a panel in the field of the roof.
Installation Approach
Symmetrical
Both vertical legs on symmetrical panels are the same. This feature allows for individual panel replaceability after installation and solves a long-standing industry challenge. Additionally, these panels allow contractors to start at any (or multiple) points on the roof providing greater flexibility during installation.
Non-Symmetrical
The legs for non-symmetrical panels are different. This feature requires non-symmetrical panels to be installed progressively, typically left to right. Consequently, non-symmetrical systems can require the removal of unaffected panels during building repairs or modifications.
Curved Roofing
Curved Metal Panels
Curves are in! McElroy Metal offers five distinct standing seam systems that can be curved right on the
Standing Seam Roofing Systems
Standing seam systems are used for a wide range of applications and projects. These systems feature interlocking seams that connect panels, giving the roof a distinct, and attractive, appearance. Furthermore, standing seam systems are manufactured from high-end steel or aluminum offering years of low-maintenance service life.
McElroy Metal standing seam systems are durable and weathertight, making them ideal for most any application.
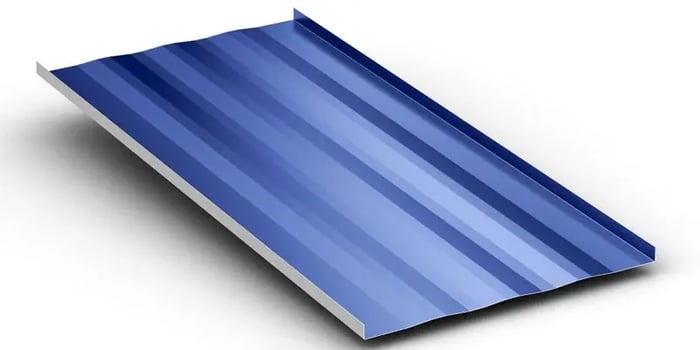
With an opportunity to choose from three distinct Maxima profiles: Maxima, Maxima 1.5 and Maxima ADV, McElroy’s Maxima family of products represents the industry’s broadest selection of vertical leg standing seam systems. While not utilized extensively for residential applications, Maxima is a great option for homes along coastal areas where high strength and wind resistance is important.
138T and 238T systems are classified as symmetrical standing seam systems and offer many advantages over traditional standing seam panels. Due to the symmetrical standing seams, individual panels can be removed and replaced in the event of damage. McElroy Metal's Shingle Recover System features the 138T panel and is an economical and energy efficient method to recover an existing shingle roof.
MasterLok-90 (also referred to as ML-90) is a snap together trapezoidal standing seam system and MasterLok-FS is a mechanically seamed trapezoidal system. Both are designed for projects with slopes as low as 1/4:12.
MasterLok-FS (also referred to as ML-FS) is a mechanically seamed trapezoidal standing seam system also designed for projects with slopes as low as 1/4:12.
Medallion I and Medallion II are older models of architectural standing seam systems and utilize separate batten caps that are installed over adjoining roofing panels. Medallion I features a narrow batten cap while Medallion II features a wider cap. Both Medallion systems are installed over solid decking. These panels are better suited for application like eyebrows over windows or other accent installations. For most homeowners, newer standing seam models such as Meridian or Medallion-Lok are a better option in terms of weather resistance and performance.
With an opportunity to choose from three distinct Maxima profiles: Maxima, Maxima 1.5 and Maxima ADV, McElroy’s Maxima family of products represents the industry’s broadest selection of vertical leg standing seam systems. While not utilized extensively for residential applications, Maxima is a great option for homes along coastal areas where high strength and wind resistance is important.
138T and 238T systems are classified as symmetrical standing seam systems and offer many advantages over traditional standing seam panels. Due to the symmetrical standing seams, individual panels can be removed and replaced in the event of damage. McElroy Metal's Shingle Recover System features the 138T panel and is an economical and energy efficient method to recover an existing shingle roof.
MasterLok-90 (also referred to as ML-90) is a snap together trapezoidal standing seam system and MasterLok-FS is a mechanically seamed trapezoidal system. Both are designed for projects with slopes as low as 1/4:12.
MasterLok-FS (also referred to as ML-FS) is a mechanically seamed trapezoidal standing seam system also designed for projects with slopes as low as 1/4:12.
Medallion I and Medallion II are older models of architectural standing seam systems and utilize separate batten caps that are installed over adjoining roofing panels. Medallion I features a narrow batten cap while Medallion II features a wider cap. Both Medallion systems are installed over solid decking. These panels are better suited for application like eyebrows over windows or other accent installations. For most homeowners, newer standing seam models such as Meridian or Medallion-Lok are a better option in terms of weather resistance and performance.
Discover the Benefits of Standing Seam Metal Roof Panels
Read the free ebook - 18 Ways to Reduce Risk With Standing Seam Metal Roof Panels.
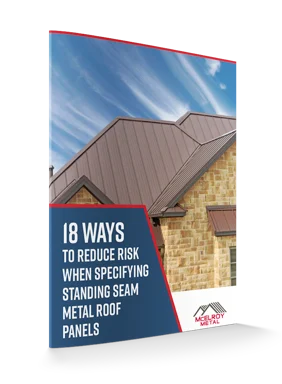
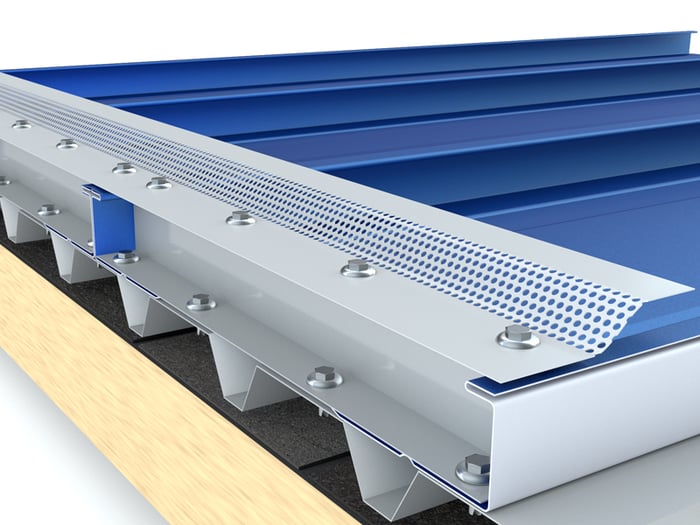
Standing Seam Retrofit Systems
McElroy Metal is the industry leader when it comes to retrofit systems. McElroy’s retrofit offerings include flat-to-steep slope, Metal-over-Metal and Metal-over-Shingle solutions. We'll ensure you can find a cost-effective and viable metal retrofit system to fit individual needs.
Our retrofit system offerings include:
- 138T Shingle Recover – Can be installed directly over existing shingles and delivers energy-saving Above Sheathing Ventilation (ASV), making the system a terrific choice for both commercial and residential projects.
- 238T Metal-Over-Metal Recover – As the name implies, the existing roof panels remain in place for metal over metal recover systems. Skipping the tear off step not only saves building owners time and money but perhaps more importantly, their daily business operations aren't impacted. These systems feature a symmetrical 238T standing seam panel and are proven to last two to four times longer than single-ply recover.
- Low Slope to Steep Slope – We offer retrofit assemblies that are easy to erect and are a great way to convert worn out flat roofs into functional and highly attractive steep slope roofs.
Our retrofit systems offer customers and building owners viable and cost effective solutions for worn out existing roofs. McElroy Metal’s experience technical staff is available to help customize retrofit solutions, so give us a call. We are always happy to help develop creative and functional solutions with metal!
Advantages of Standing Seam Metal Roofing
Concealed Fasteners
Standing seam systems attach to the substructure with concealed fasteners. Since there are no exposed screws with washers than can shrink or crack over time, they are considered a more weather-tight system than exposed fastener systems.
Expansion/Contraction Ability
Standing seam systems allow expansion and contraction through either a clip or slotted flange. Conversely, exposed fastener systems are pinned which can result in the fastener hole elongating over time and allowing water penetration. Check this out to learn more.
On-Site Panel Production
Some manufacturers (McElroy Metal included) can produce standing seam panels on-site in lengths up to 250’. Single-piece panels are quicker to install, more weathertight and require fewer components making them a superior and often more economical system.
Aesthetics
Standing seam panels typically offer a distinct vertical leg. This tall vertical leg can offer a nice shadow effect and the illusion of a flat pan in between the major ribs which many architects and building owners prefer.
Extensive Testing
In order to meet stringent building codes and life safety issues, standing seam panels are subjected to more testing than exposed fastened type systems. Standard tests include uplift, air and water, impact, and fire resistance.
Weather Tightness Warranties
While additional charges and criteria typically apply, standing seam systems can often offer Weather Tightness Warranties where exposed fastener panel systems cannot.
The Latest on Standing Seam Metal Roofing on our Blog
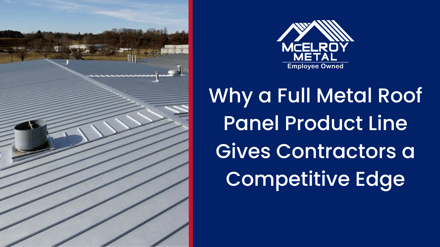
Why a Full Metal Roof Panel Product Line Gives Contractors a Competitive Edge
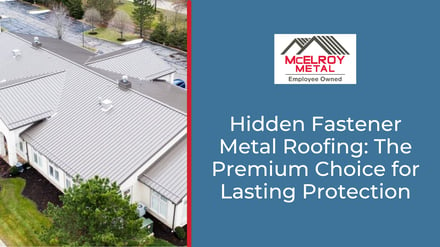